
Description
The Intelligent Infrastructure Laboratory is a flexible space which includes structural asset testing area, 10T Crane, 750mm thick reinforced concrete slab, with an array of 300kN anchor points at 750mm spacings, easy access large external doors and convenient driveway with unloading area to ensure suitable transportation access to the facility for large scale and heavy elements of infrastructure. The laboratory allows real scale full size experiments and testing of infrastructure elements. This covers both inherited infrastructure for safety and maintenance purpose testing and future infrastructure elements, for developing the next generation of above and underground infrastructure and other capital-intensive national infrastructure assets.
Vision
The Intelligent Infrastructure Laboratory is managed by the Structural Engineering Group. (SEG). All the facilities in the Lab prioritize large-scale and medium-scale testing, which is central to their translational research and consultancy efforts. By validating the large-scale performance of optimised components (such as concrete beams) and evaluating the resilience of existing structures (such as masonry arch bridges), they contribute to three key objectives of the SEG vision:
- Build Efficient
- Build Safe
- Build Sustainable
Key equipment
One of the main features of the laboratory is its strong floor, equipped with numerous anchorage points that enable flexible positioning of actuators and testing frames in various configurations. This adaptability allows the laboratory to accommodate a diverse range of structural experiments while minimizing interference and optimizing workflow efficiency.
The testing equipment has been employed for several research, Knowledge Exchange and consultancy projects, funded by EPSRC or various UK companies such as Network Rail, MetLase, Unipart Construction Technologies and Rochester Bridge Trust.
1) Large testing frame
The testing apparatus comprises no.2 hydraulic actuators, each with a capacity of 2MN and 600mm travel and various cross beams, spreader beams and supports to adapt to different types of tests. The actuators are bolted on the strongfloor and are connected together via a cross beam to work as a pair. The test rig is capable of delivering compressive/tensile, shear, torsion tests on specimens up to 10T in weight and 12m in length. Examples of these type of tests are shown in the images below.
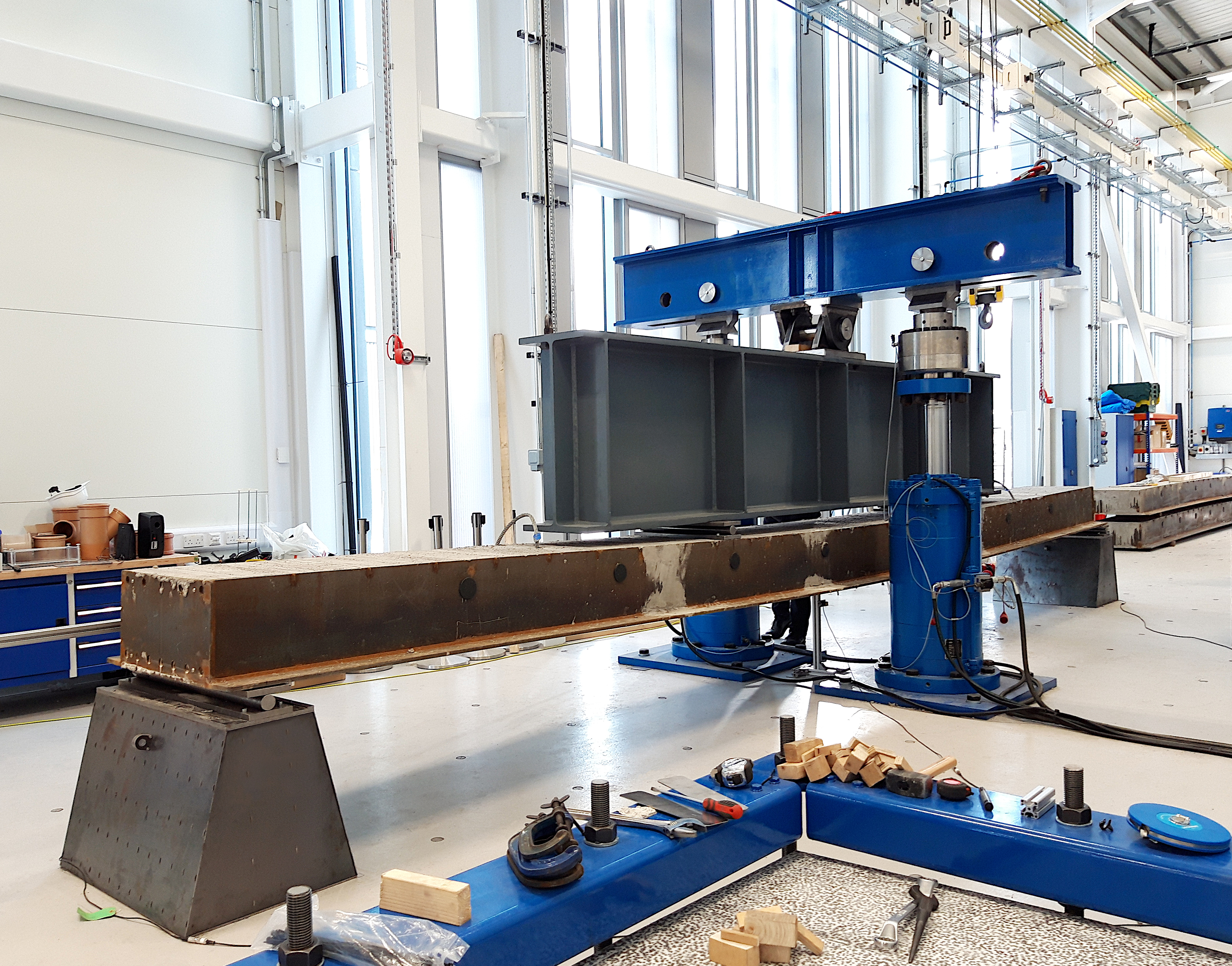
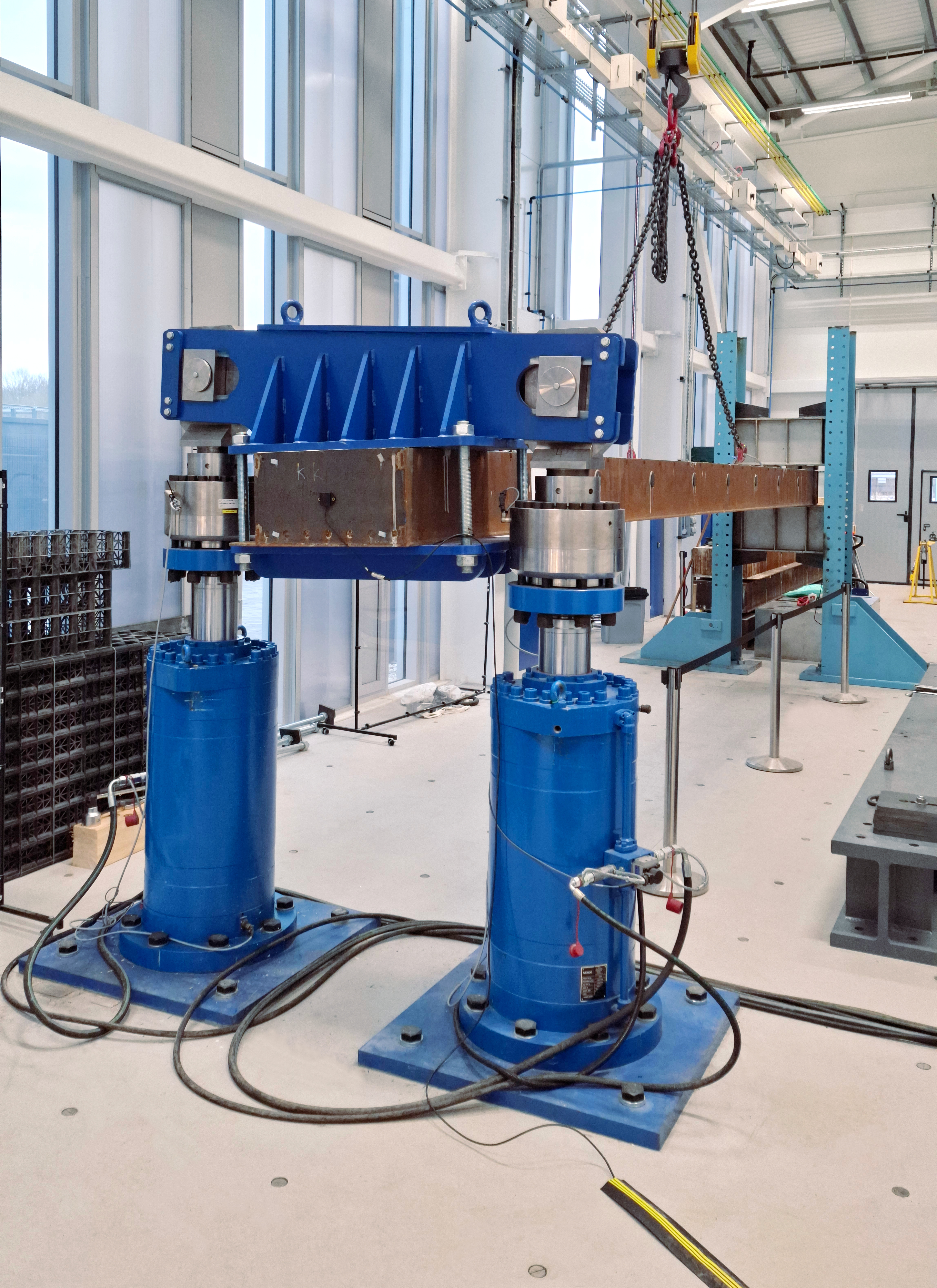
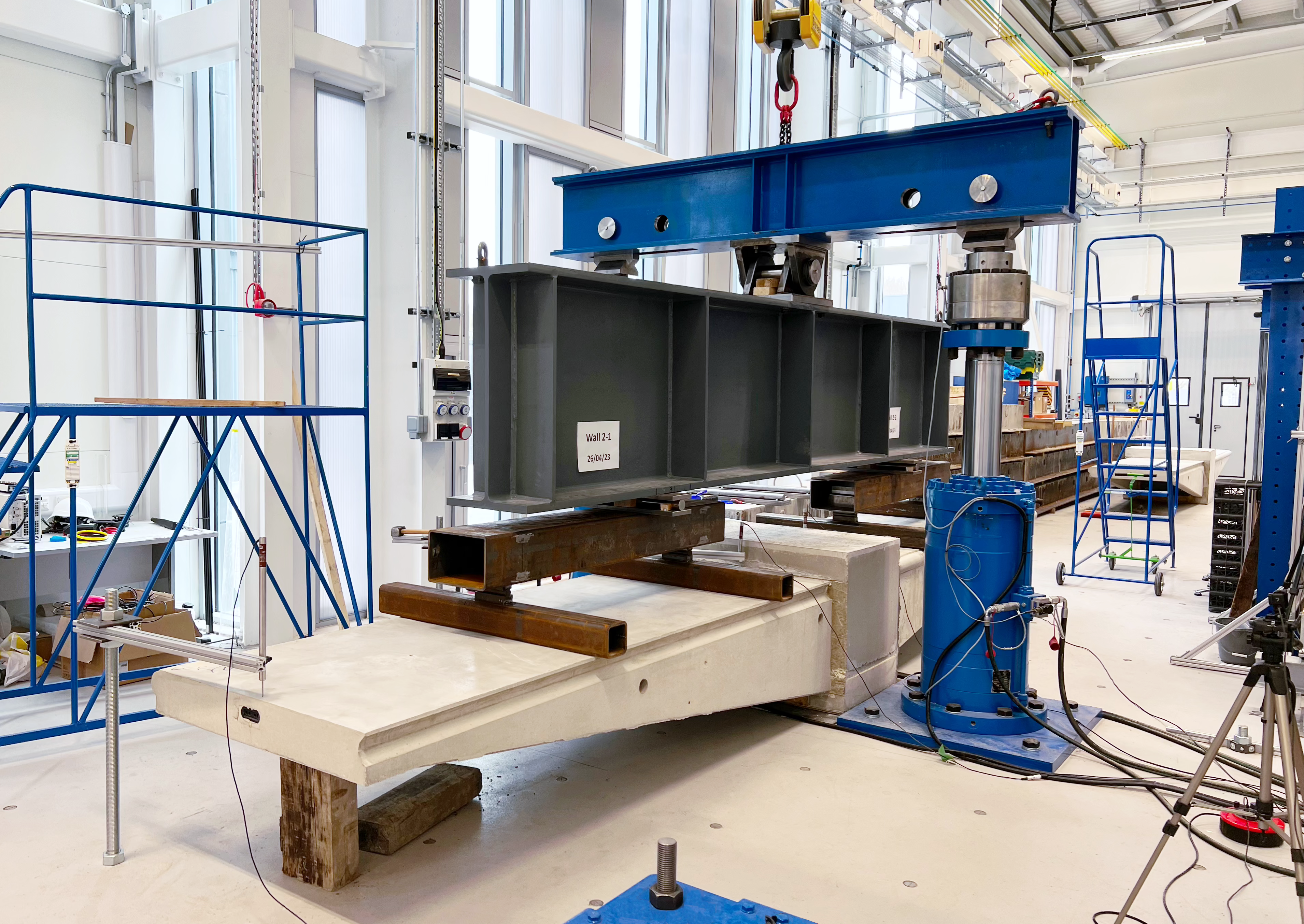
2) Medium testing frame
The medium testing frame includes a set of no.3 reaction frames and actuators, each with 250kN capacity and 500mm travel. The actuators can be used individually or in conjunction and are operated via a 3-channel Cubus control system. The test rig is intended for compressive/tensile, shear and cyclic loading.
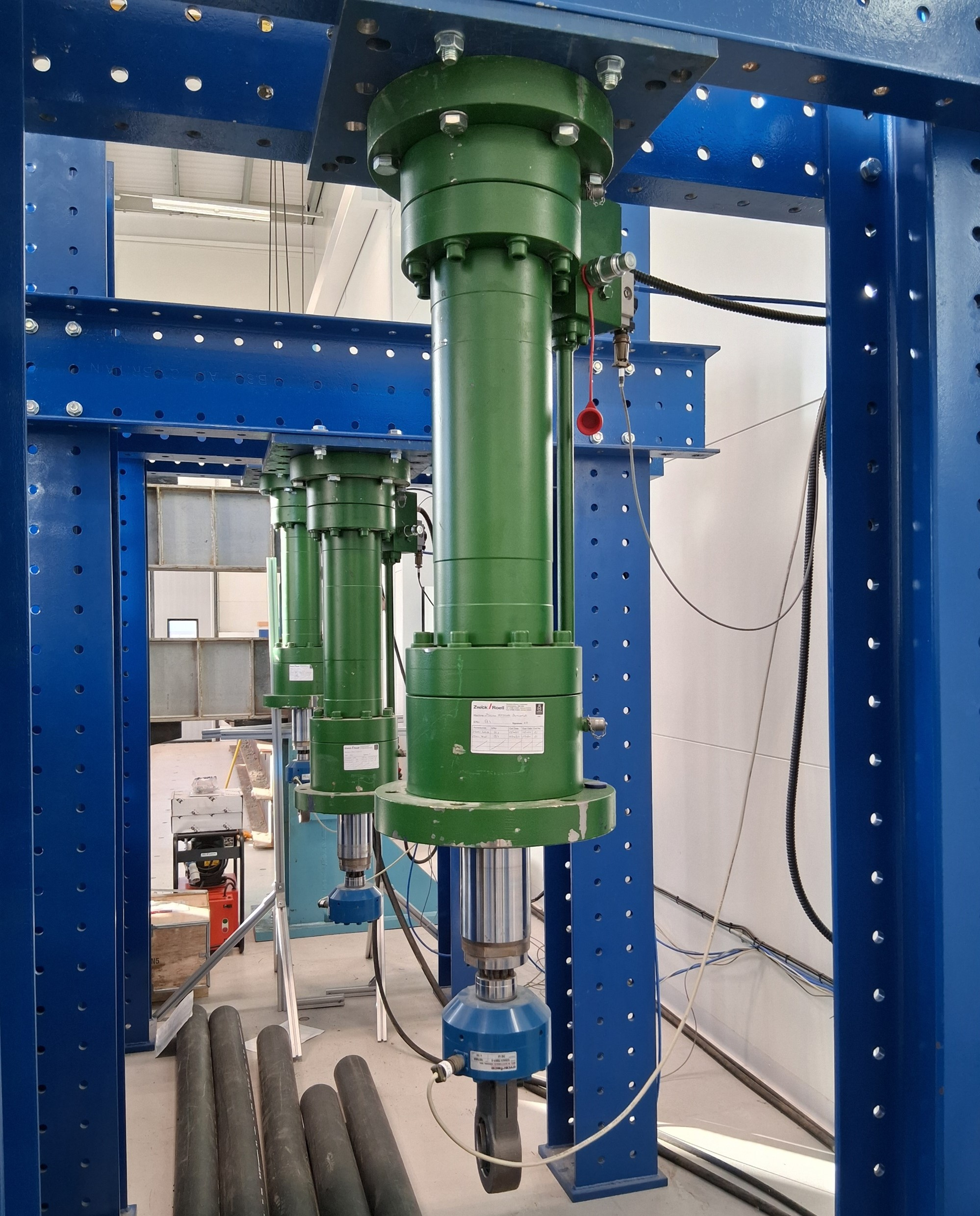
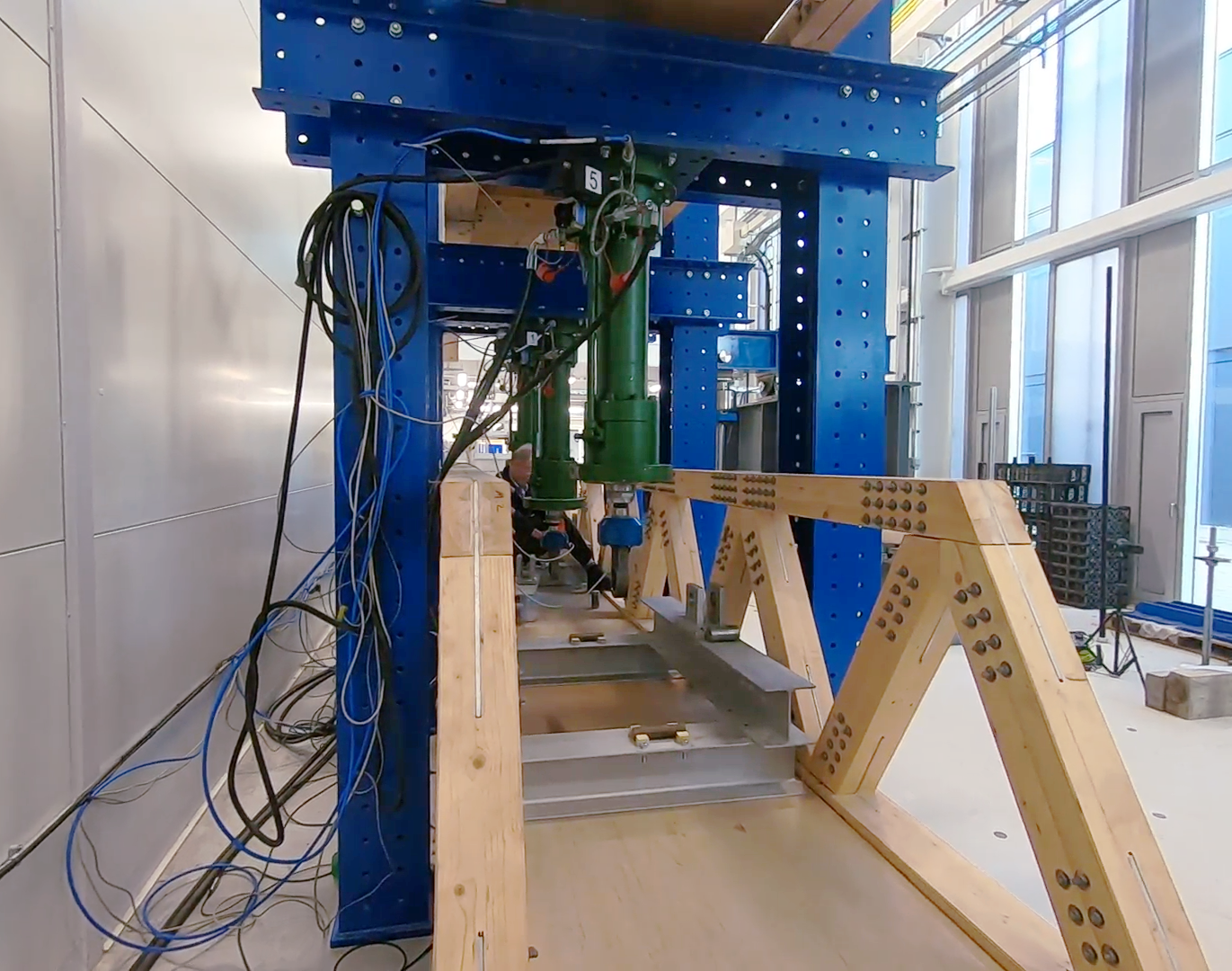
3) Slab Test setup
A test frame designed for multipoint loading of 2m x 2m concrete slabs or grillages. Loads are applied via no.9 hydraulic actuators of 10T capacity each that can be used together or individually.
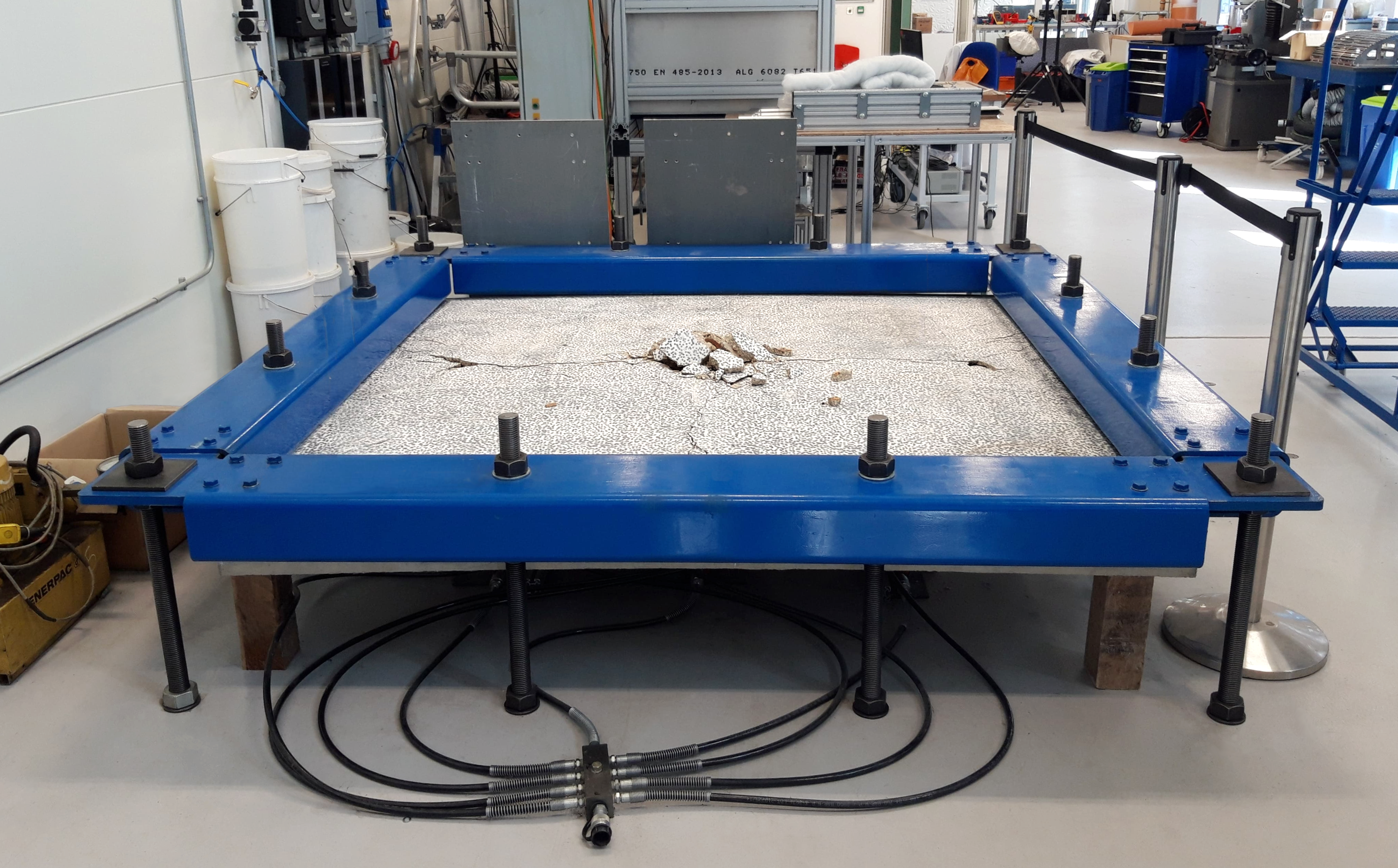
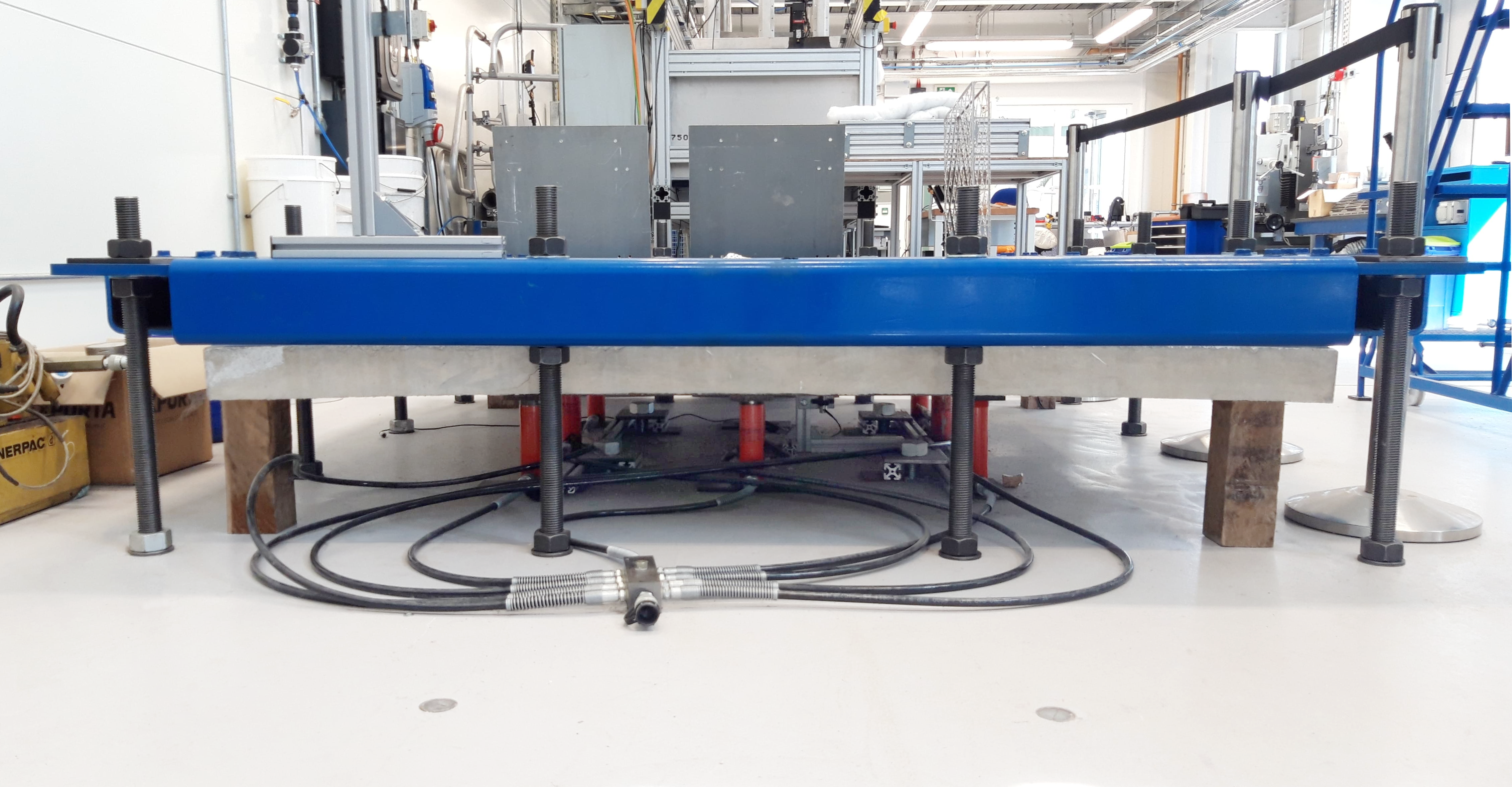
4) Masonry Arch test setup
The setup is designed to test medium-scale masonry arch bridges with various geometries and backfill types, including masonry and sand infill. The test rig includes an automated pluviation system for sand deposition to ensure consistent sand density. Laser-cut steel centerings allow precise construction of both square and skew arch barrels. The rig loading system consists of an electric actuator operated in displacement control mode and no.2 RDP tension/compression load cells with 2.2kN range and 8.9kN range.
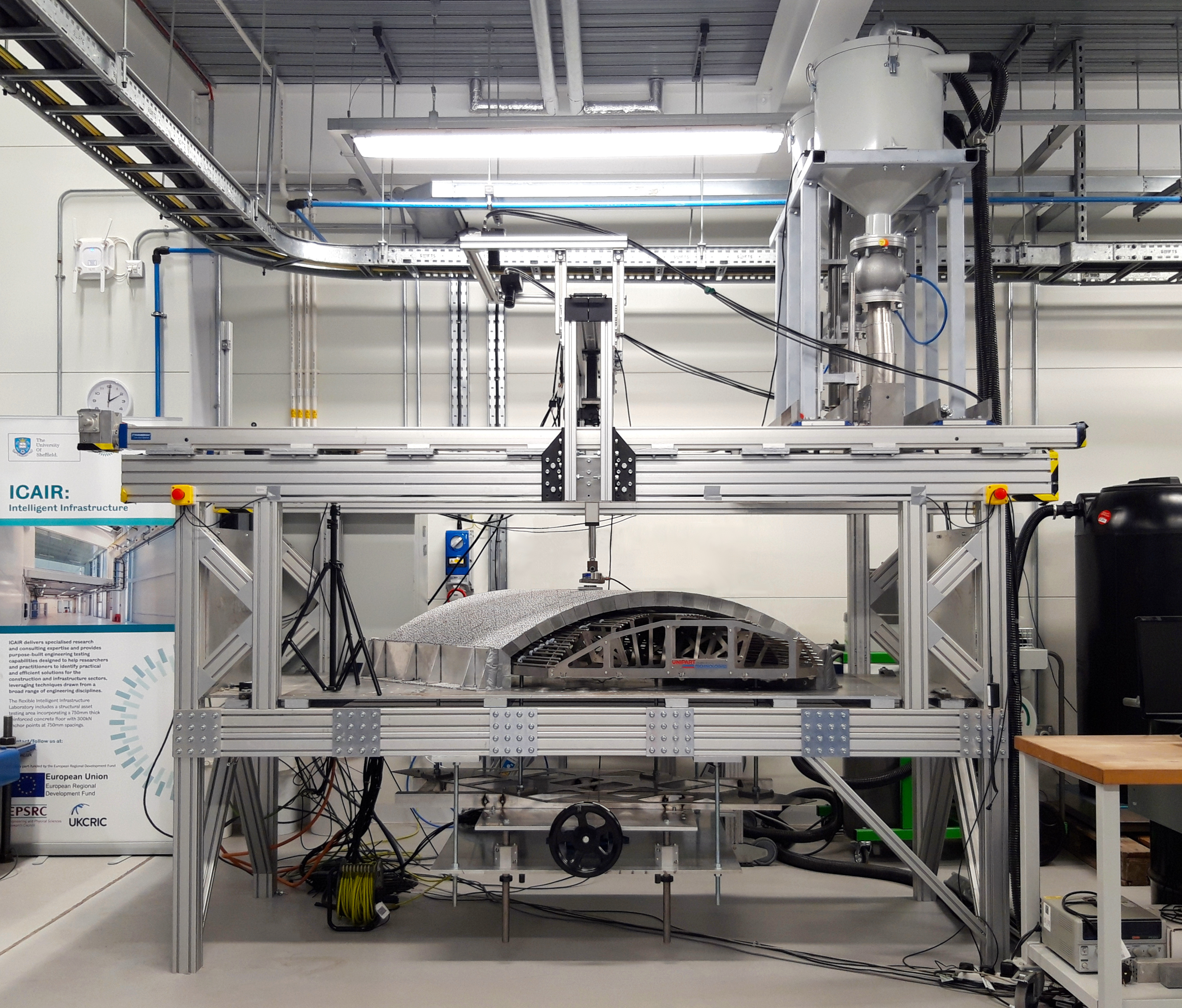
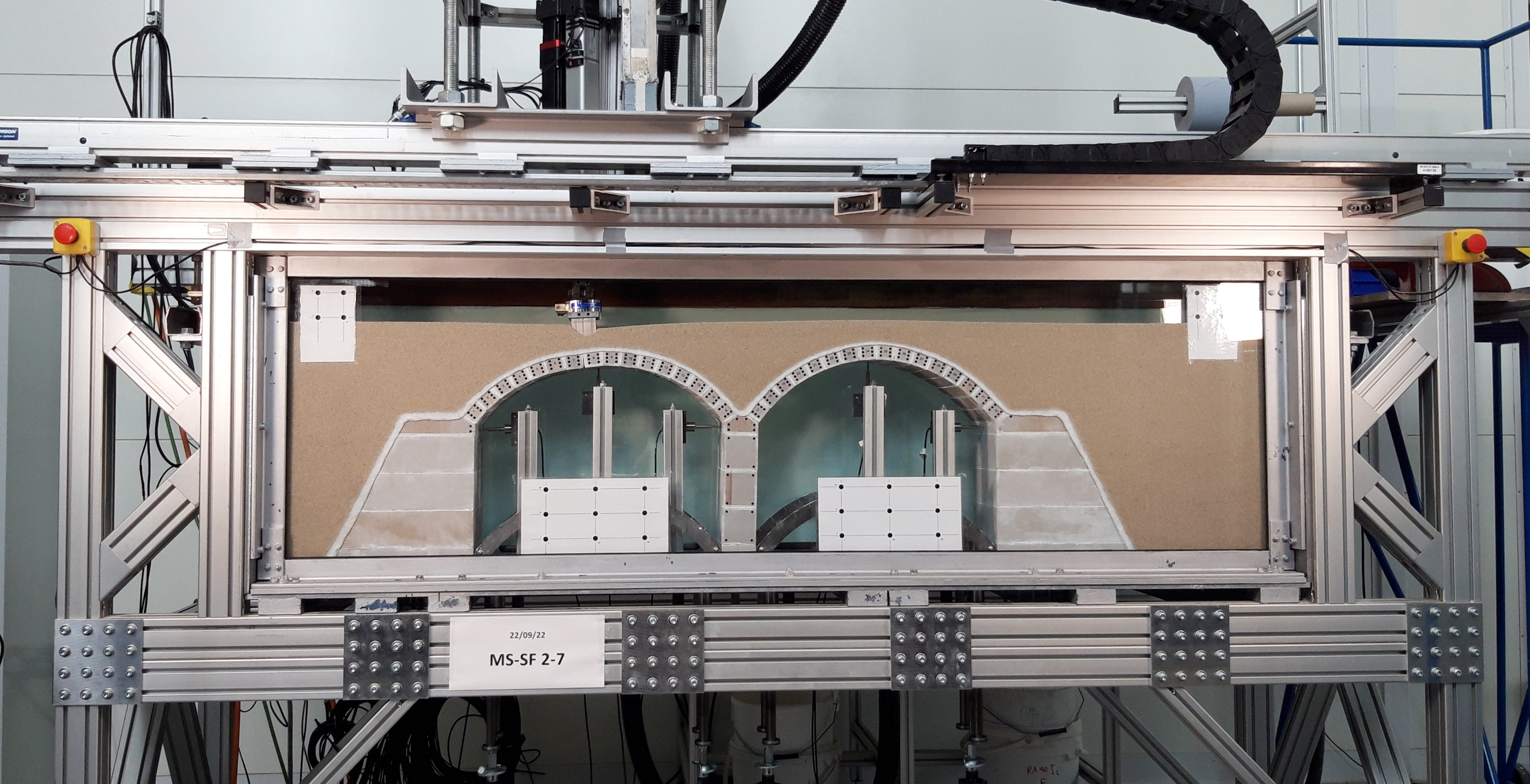
The equipment at the Intelligent Infrastructure Laboratory also includes:
- High-precision RDP LVDTs for measuring displacements (with 25mm, 50mm and 100mm travel);
- HG-C1200 laser gauges for measuring displacements (200mm detection range);
- Tilt gauges for measuring rotations;
- Dantec 3D Digital Image Correlation (DIC) system for accurate measurement of displacements and strains;
- GoPro Hero7 4k video cameras to record tests;
- Canon DSLR camera to take high resolution digital images of tests.
5) Workshop
The Intelligent Infrastructure Laboratory also includes a small workshop area containing a milling/drilling machine, saw, marking out table, benches and a variety of hand tools. It is used for the manufacture of small components, frames and supports to assist testing. A small electronics bench is also present in this area. Large components can be manufactured in the workshop located in Sir Frederick Mappin building.